Plastic Extrusion Applications
Plastic extrusion is the most widely used high volume manufacturing processes for the forming of regular plastic and thermoplastic material. Using an extrusion process, Plastic Extrusion Technologies creates objects such as plastic parts for deck railings, window frames, wire insulation, weather stripping, thermoplastic coatings and more.
Plastic Extrusion Technologies manufactures plastic products for all types of companies from window manufacturers to adhesives producers, from startup ventures looking to get a prototype, to established companies that want to cut their costs. Our custom plastic extrusions provide solutions to many different companies across the country.
Click to view some of our work in these cities:
Learn more about our plastic extrusion applications by clicking the links below:
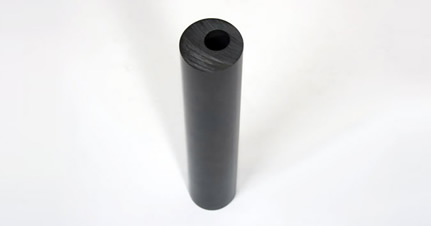
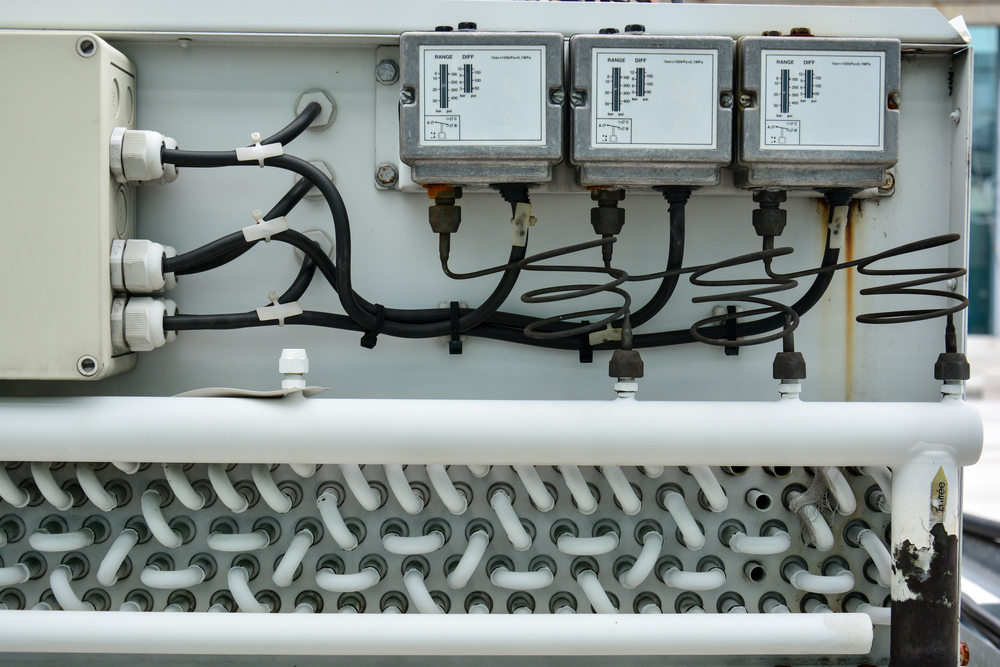
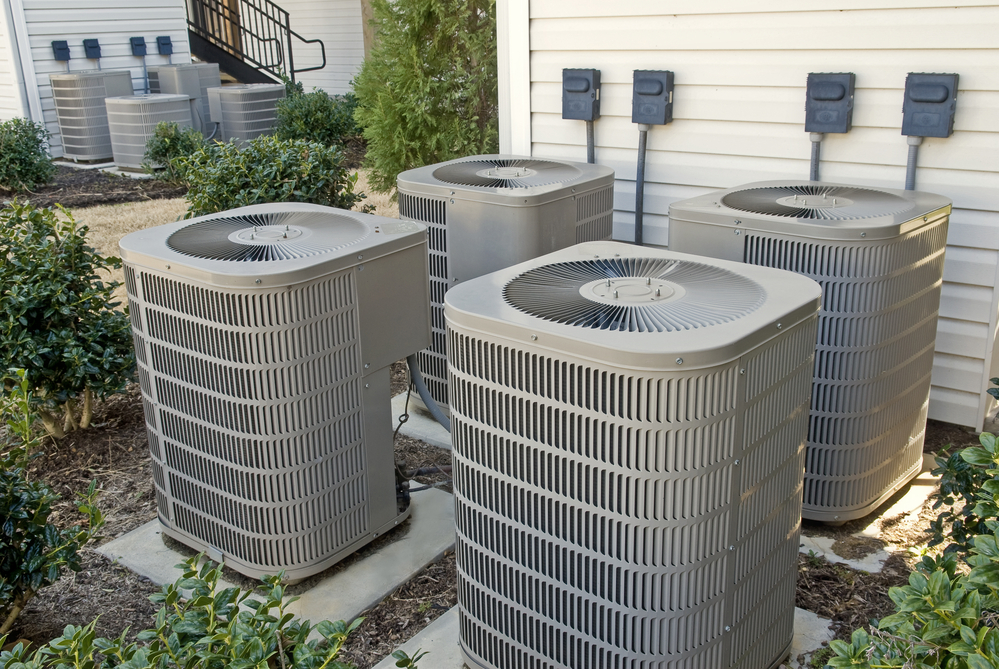
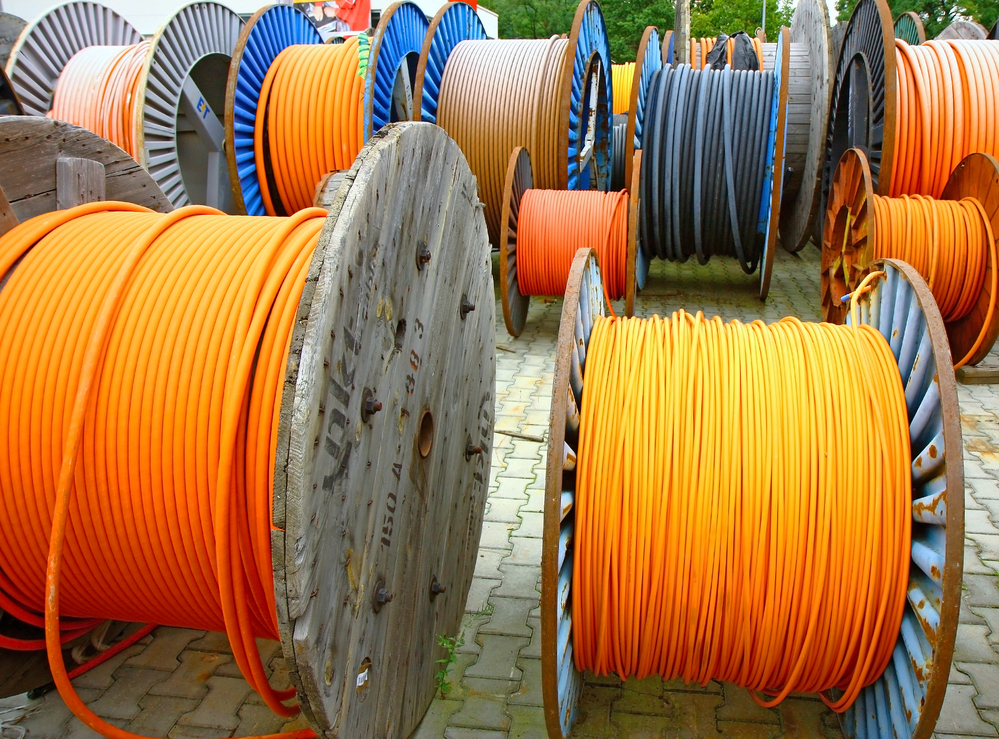
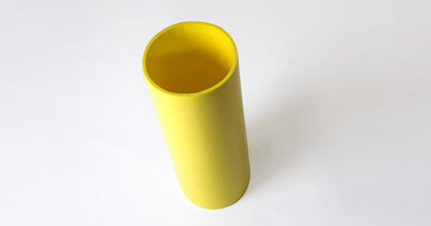
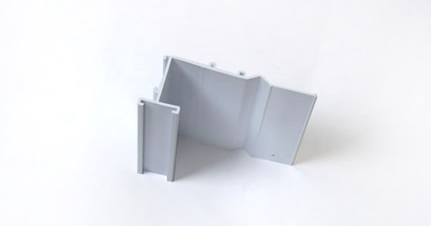
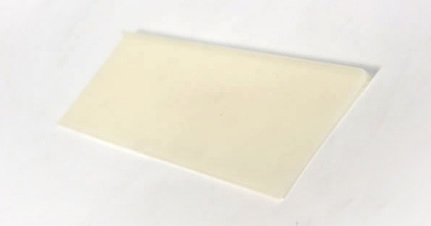
If you are looking to cut costs, increase efficiency, or plan to start a new plastic extrusion project, use the best company in the industry with over 100 years of successful experience – Plastic Extrusion Technologies. Contact our team of specialists to learn more about our products, abilities and applications.