Custom Plastic Extrusions
BETTER QUALITY.
FASTER DELIVERY DATES.
Plastic Extrusions for Every Application
Plastic Extrusion Technologies is a manufacturer that can meet all your custom plastic profile and plastic tubing extrusion needs throughout the United States. We manufacture everything from point of purchase signs to standard plastic profiles to automotive plastic parts.
Extrusion stands out in the realm of plastics manufacturing, offering unique advantages. It is a versatile technique accommodating a vast spectrum of plastic materials. Unlike traditional plastic injection molding, extrusion can continuously shape molten plastic to desired specifications.
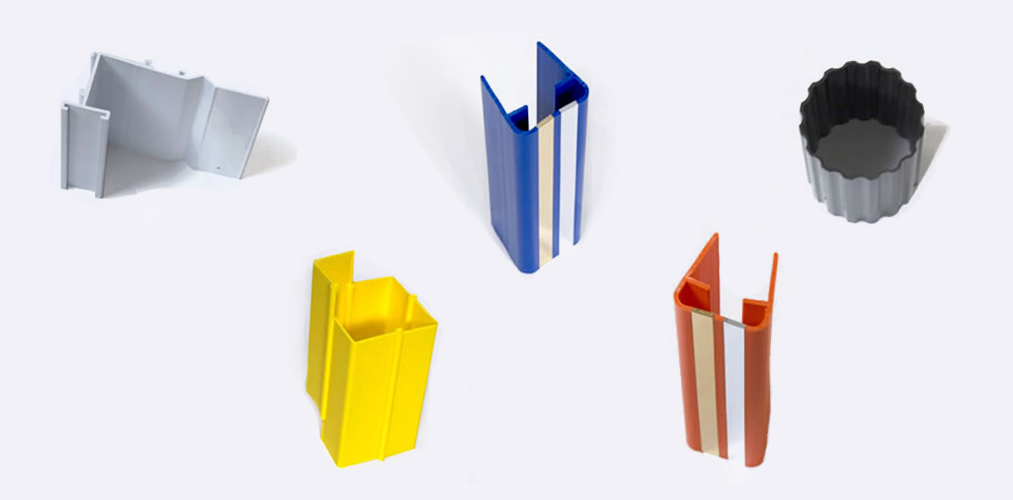
The Plastic Extrusion Process
Harnessing plastic extrusion technology requires a symphony of skills. At its core, the procedure seems straightforward, but it demands precision. To craft custom plastic extrusion products, companies like Plastic Extrusion Tech use an advanced plastic extrusion machine.
Here’s a snapshot of how we transform commodity plastics into tangible plastic parts:
1. Feeding: The plastic extruder, whether a single screw extruder or a twin-screw extruder, starts by taking in thermoplastic resin. These resins, either beads or pellets, might include materials like low-density polyethylene or thermoplastic elastomer.
2. Melting: As the polymer enters the extrusion line, the plastic extruder melts it into a polymer melt.
3. Shaping: The molten plastic then journeys through a die, functioning as a mold. The breaker plate ensures an even flow before it reaches the die. This stage dictates the final shape of the plastic product (plastic film, plastic sheet).
4. Cooling & Finalizing: Post extrusion, cooling rolls stabilize the freshly shaped material. Thereafter, it’s cut, prepared, or 3D printed based on the requisite specifications.
With Plastic Extrusion Tech’s advanced extrusion machine and expertise, the potential is limitless. From wire insulation and stock plastic extrusions to unique tooling for plastic parts, our extrusion line integrates the best of plastic extrusion work. Notably, we’re not confined to just plastic; our capabilities extend to aluminum extrusion as well.
The plastic extrusion process is wide and varied and can take many different forms, including:
Being the most common type of extrusion in the industry, single extrusions are by far the most common type of plastic extrusions where profiles are designed using a single thermoplastic material cut to varying lengths. Plastic Extrusion Technologies has the capability to produce a wide gamut of profiles, from the very simple to the very complex. We also offer secondary processes such as Notching and Drilling, Plastic Gluing and Taping, Punching, Forming, and Heat Welding.
Our state-of-the-art plastic tubing extrusion processes allow us to hold the industry challenging tolerances and manufacture extrusions using a broad range of thermoplastic materials to meet your exact specifications and exceed your highest expectations. We are committed to the strictest quality standards, continued investments in the latest equipment, and client service that is second-to-none.
Coextrusion options are available as well. This type of extrusion utilizes two or more extruders to melt and deliver a steady volumetric throughput of different viscous plastics to a single extrusion head (die), which extrudes the materials into the desired form. The thickness of each layer is determined by the relative speed and size of the individual extruders delivering the materials.
Materials We Use
Rigid PVC – strong, low-cost plastic material that is extremely easy to fabricate.
Polyethylene – lightweight, durable thermoplastic with variable crystalline structure.
High Impact Polystyrene (HIPS).
Polypropylene – a thermoplastic polymer.
Polyurethane – polymer composed of organic units connected by urethane links.
Acrylic – petroleum-based thermoplastics.
Polycarbonate – thermoplastic polymers containing carbonate groups.
Flexible PVC – soft plastic material ranging from transparent to opaque.
Noryl – non-reinforced blend of polyphenylene ether and high impact polystyrene.
TPR – modified from Styrene-butadiene-styrene Block Copolymer (SBS).
ABS – impact-resistant engineering thermoplastic & amorphous polymer.
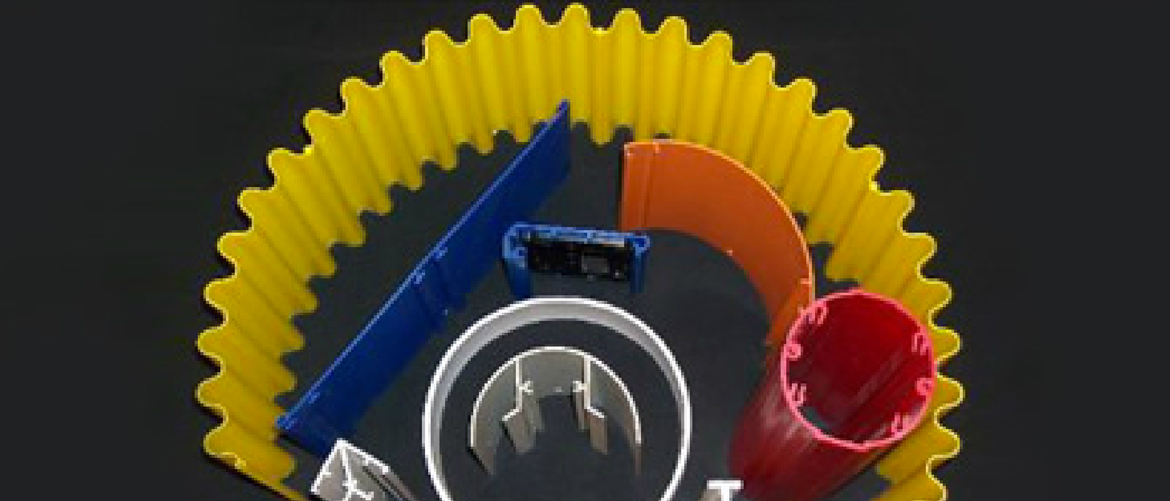
Contact Us Today To Experience A
Superior Plastic Extrusion Process
Plastic Extrusions Portfolio Gallery
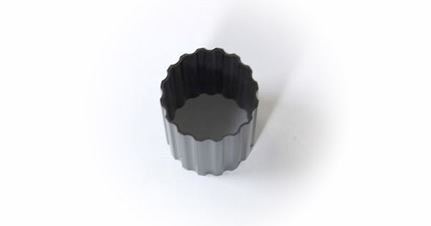
Fluted Tube, Rigid PVC
These tubes were used as covers for parking meter poles to provide protection from the weather. These keep expensive parking meters protected from the elements.
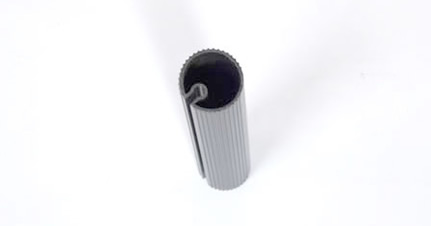
Ribbed Handle, Rigid PVC
This product was part of a squeegee application. These ribbed handles can be used to clean car windows and be placed on cleaning tools to clean water from windows and floors.
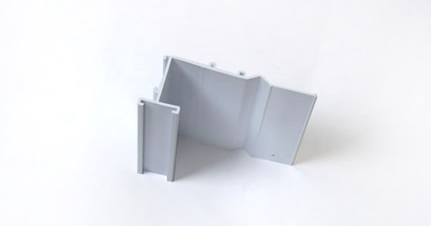
Plastic Extrusions Frame, Rigid PVC
Plastic Extrusion Technologies manufactured this rigid PVC frame for a client based in New Jersey. These frames were used to provide a structure for a point of purchase product display for stability.
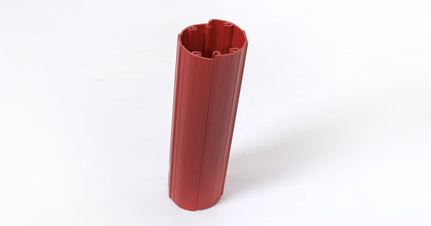
Interlocking Profile, Rigid PVC
Plastic Extrusion Technologies provided a rigid PVC interlocking profile for a client in New York. This profile was used for a commercial product application.
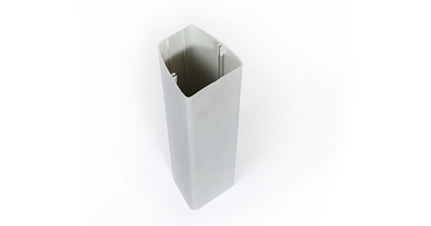
Pedestal, Rigid PVC
Plastic Extrusion Technologies provided rigid PVC pedestals for a New Hampshire client. This product was for a commercial product application.
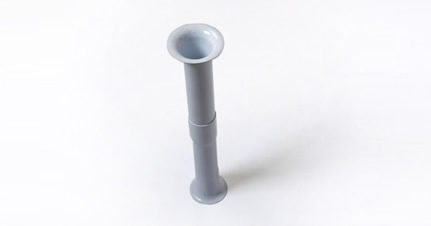
Flared Handle, Rigid PVC
PVC is one of the most popular plastics, used heavily in the packaging industry because if its light weight and durability.
Custom Extruded Profiles
Our profiles can produce custom shapes to meet your needs, and our multi-line operation allows for easy production of small and large plastic profiles, ranging from 1/32” to 13”. Plastic Extrusion Technologies produces custom profiles, from the simple to the complex.
Plastic extrusion has several advantages over other forms of plastics manufacturing like the ability to create plastic profiles of infinite length in large or small production volumes. Many different plastic products can be made in this manner out of numerous plastic materials. We also offer secondary processes such as plastic Notching and Drilling, Gluing and Taping, Punching, Forming, and Heat Welding.
We are confident that Plastic Extrusion Technologies will be the best partner for you. We will work with your current plastic extrusion tooling, or purchase new machinery for long-term engagements, to provide high-quality extruded products. Our cost effective manufacturing process is ideal for both custom extruding and high-volume plastic extrusions.
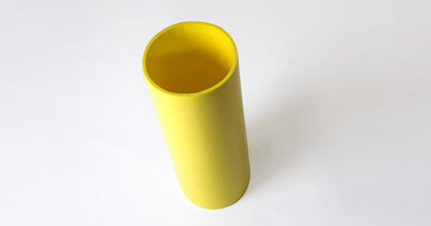
Competitive Edge
New pricing on plastic extrusion products
Higher quality
Faster delivery dates
Experienced opinion on your current design ideas
With over 45,000 square feet, our plastic extrusion facility is filled with the most state-of-the-art production machinery. We have over 100 years of experience in the industry, and the ability to produce plastic profiles of limitless length in both vast and minimal production volumes. Plastic Extrusion Technologies has the experience, technology and knowledge to assist you in the design, production and finishing of your extruded plastic profiles and plastic tubing products.